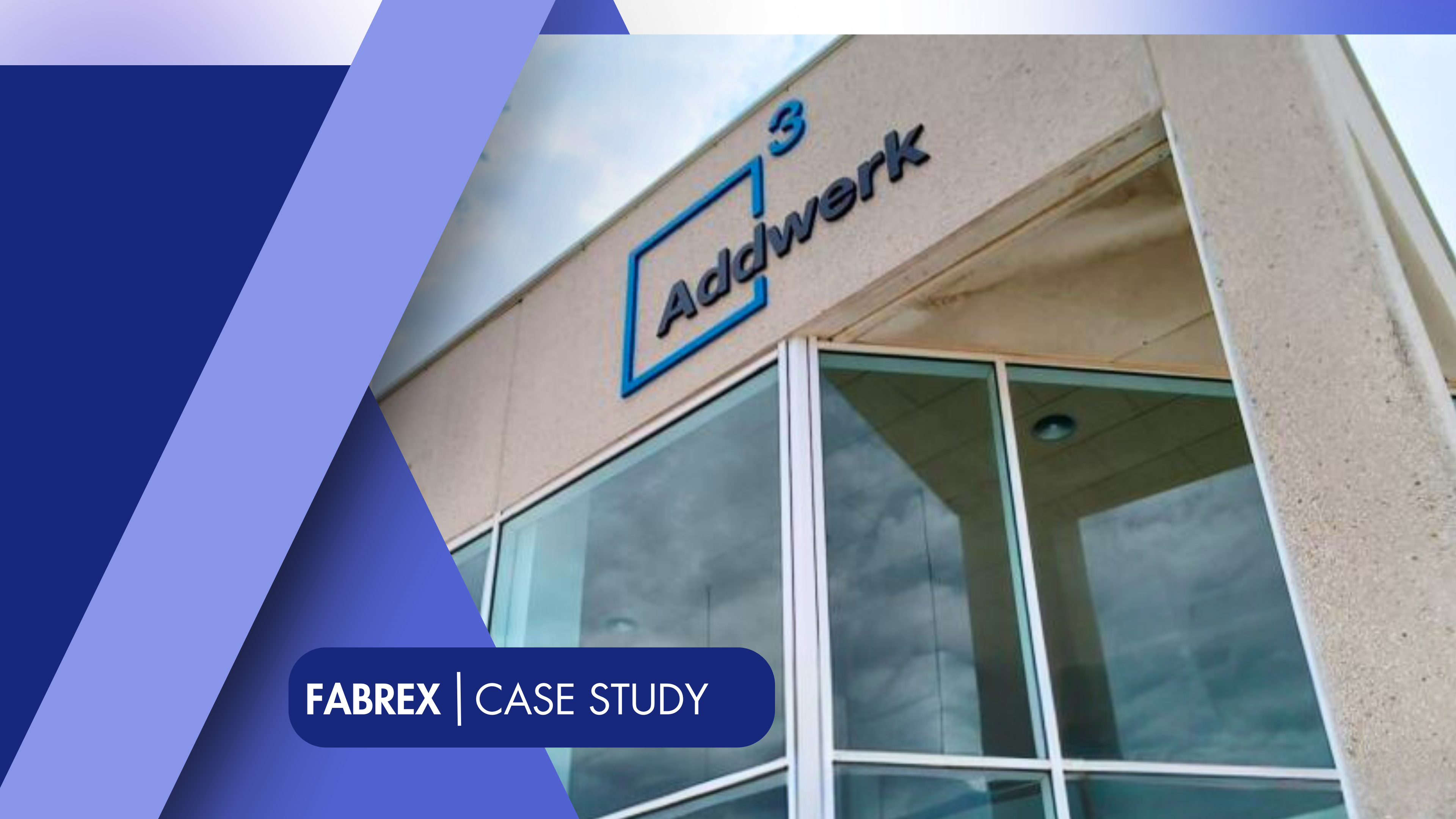
Case Study | How Fabrex’s Smart Factory Solutions Transformed Addwerk's Operations
This case study delves into how Fabrex’s innovative technology addressed Addwerk’s challenges and delivered measurable improvements in their performance and client relations.
Addwerk, a prominent service bureau in the manufacturing sector, found itself grappling with significant operational hurdles that were affecting both productivity and customer satisfaction. Faced with outdated systems and inefficiencies, they sought a solution to enhance their operational effectiveness. Fabrex’s Smart Factory Solutions provided the transformative edge they needed. This case study delves into how Fabrex’s innovative technology addressed Addwerk’s challenges and delivered measurable improvements in their performance and client relations.
Understanding Addwerk's Operational Landscape
Addwerk excels in rapid prototyping and short-run production across various industries, including automotive, aerospace, and consumer electronics. Despite their extensive expertise, the company struggled with outdated processes and disjointed systems, which compromised their ability to serve their clients effectively and efficiently.
These were the Challenges that they faced before Fabrex:
- Sales and Post-Sales Challenges: Generating quotes manually was both slow and prone to errors, resulting in delays and frustrated customers.
- Inefficient Order Management: Managing orders through various production stages was cumbersome, leading to frequent miscommunications and missed deadlines.
- Operational Inefficiencies: The absence of an integrated task management and production planning system resulted in disorganized workflows and decreased productivity.
Addwerk’s primary objective was to streamline their operations, enhance order tracking, and improve task management to boost overall customer satisfaction. Here’s how Fabrex’s solutions helped them achieve these goals:
Solutions Provided by Fabrex
Fabrex provided a comprehensive suite of solutions designed to tackle Addwerk’s specific challenges:
- Automated Quotation System: Fabrex’s system enabled instant and accurate quote generation, dramatically reducing manual effort and errors.
- Real-Time Order Tracking: QR codes allowed for seamless tracking of orders through the production process, enhancing transparency and operational efficiency.
- Advanced Task Management Module: This module introduced a structured task management system, ensuring tasks were well-defined, prioritized, and assigned effectively.
- ERP and 3PL Integration: Fabrex’s solutions integrated smoothly with Addwerk’s existing ERP and 3PL systems, automating many processes and creating a unified management approach.
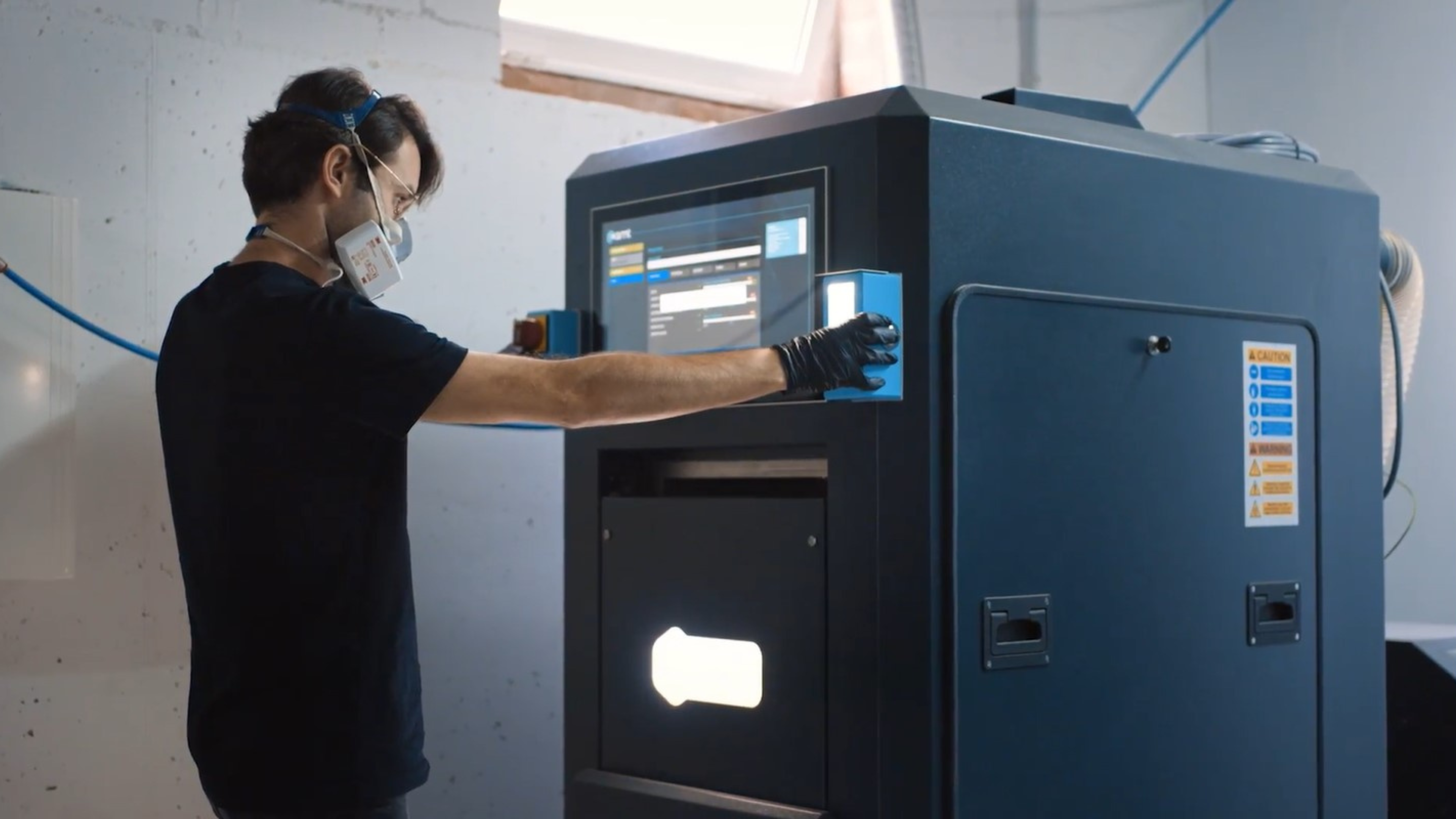
Results
The impact of Fabrex’s solutions on Addwerk was substantial, here are some metrics that show the improvement that they experienced in different areas of production.
3473
Quotes
(before 1210)
68%
Success rate
(before 59%)
1 h/day
Time spent on managing the production
(before 4 h/day)
0 h
Time spent on administration tasks
(before 5 h/day)
Now we just need a few minutes for validation
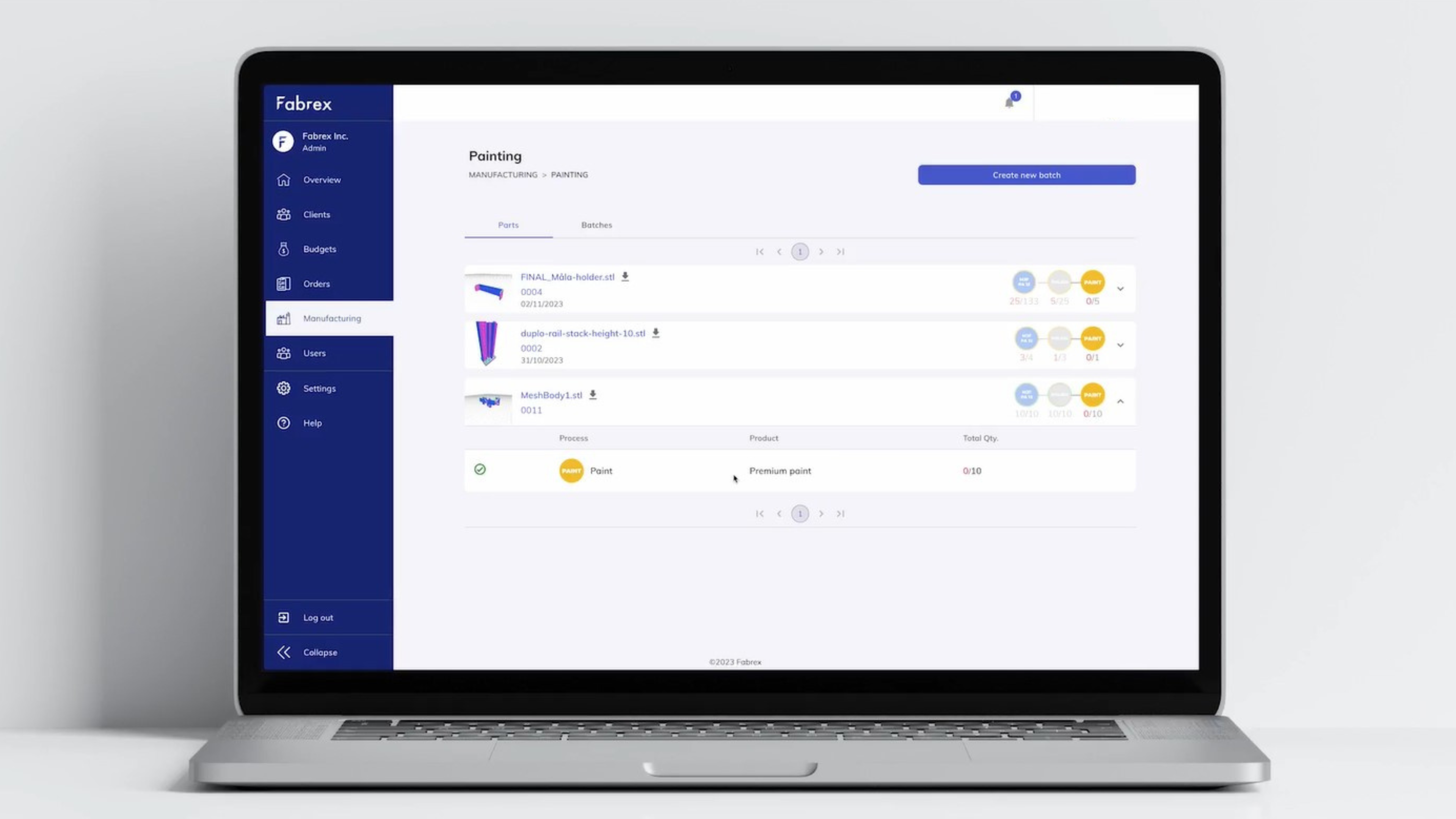
Understanding the Implementation Process
The implementation process was methodical and thorough. Here’s how we improved Addwerk’s overall operations:
- Initial assessment: Fabrex’s team conducted a detailed review of Addwerk’s existing processes to identify key areas for improvement.
- Customization: The solutions were tailored to address Addwerk’s specific needs and integrated seamlessly with their current systems.
- Training: Only a few training sessions were held to ensure that Addwerk’s staff could effectively utilize Fabrex, thanks to its easy learning curve.
- Phased deployment: The solution was rolled out in stages, beginning with the automated quotation system, followed by real-time order tracking, and ending with the task management module.
- Ongoing support: Fabrex provided continuous support throughout the transition to resolve any issues and ensure the software was used to its full potential.
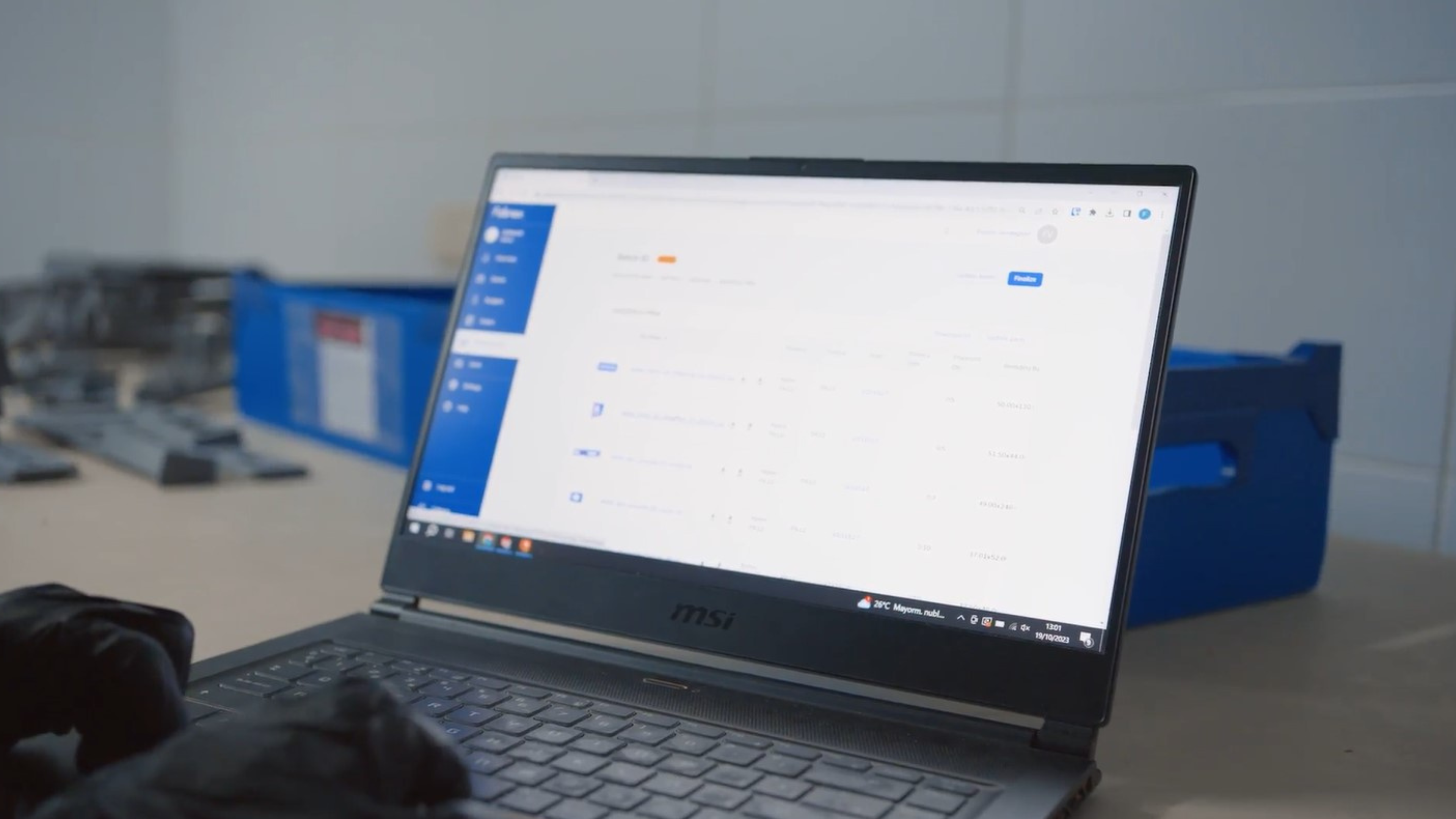
All of this has translate into:
- Increased efficiency: The transition to an automated quotation system reduced the time required to generate quotes from 2-3 days to near-instantaneous, allowing the sales team to focus on client interactions.
- Enhanced order tracking: Real-time tracking capabilities reduced production delays and miscommunications by 68%. Additionally, the customer portal allowed clients to access real-time updates on their orders, minimizing follow-ups.
- Improved productivity: The task management module streamlined workflows, leading to a high increase in overall productivity.
- Seamless integration: Integration with ERP and 3PL systems enabled Addwerk to handle complex operations efficiently with a streamlined team.
Higher customer satisfaction: The improvements in efficiency and transparency resulted in heightened customer satisfaction, with clients recognizing the faster turnaround and reliability of service.
Testimonial from Addwerk
Fabrex’s Smart Factory Solutions provided a critical overhaul of Addwerk’s operations, addressing their main challenges and driving significant improvements in productivity and customer satisfaction. By modernizing their processes, Addwerk is now better equipped to meet client demands and maintain a competitive edge in the industry.
For businesses that have similar operational issues, Fabrex’s solutions offer a strategic approach to streamlining processes and achieving operational excellence. Explore how Fabrex can drive transformation in your organization by visiting our website and scheduling a demo.
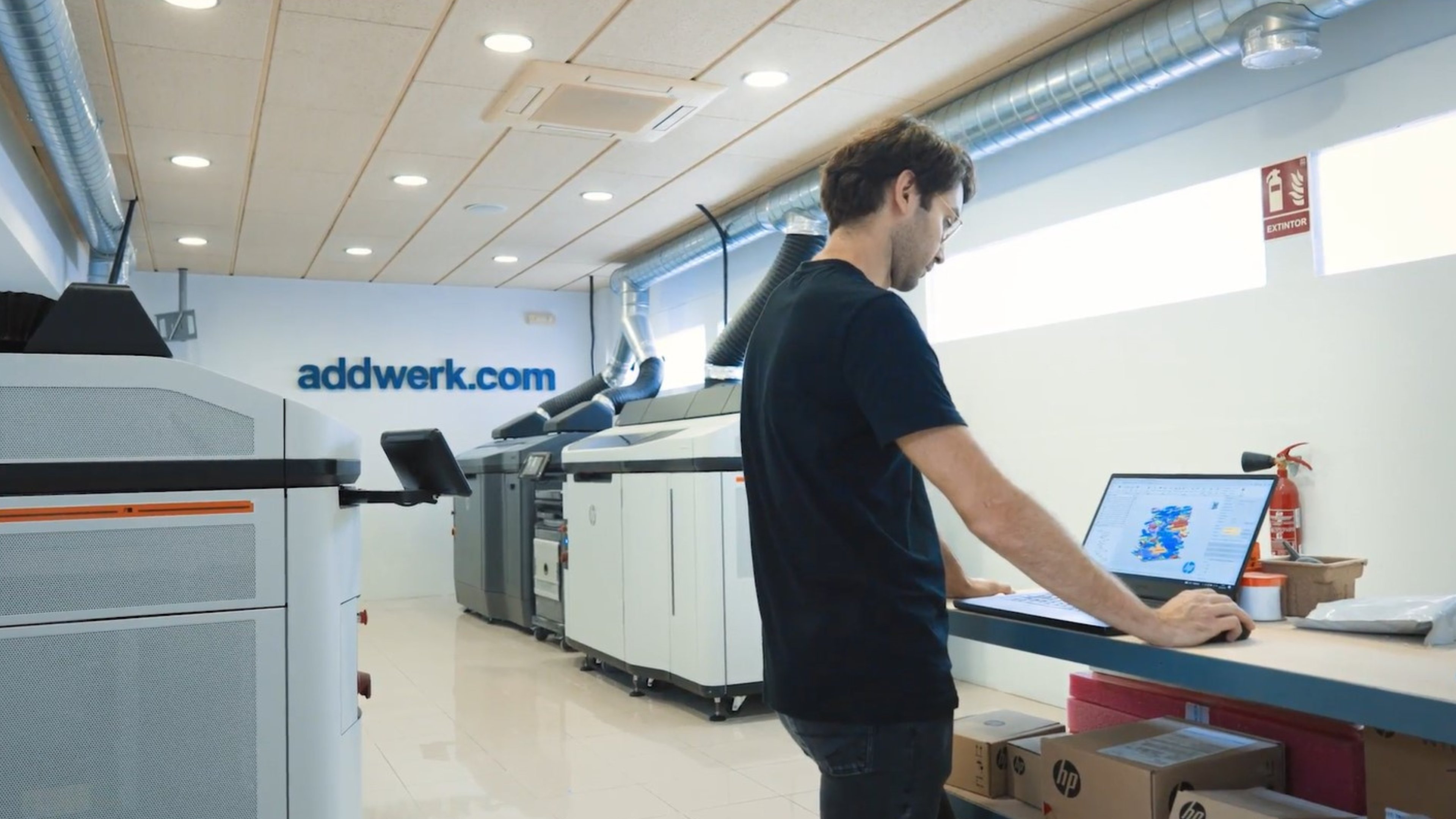